Pallet Racking
Is your warehouse overrun with pallets and other materials on the shop floor?WAREHOUSE PALLET RACKING SUPPLY & INSTALL
NEW PALLET RACKING FOR SALE
Pallet racking is the most common application found in warehouses that store and distribute palletised products. These systems come in all shapes and sizes designed to suit virtually any pallet specification and building dimensions when used with the correct materials handling equipment, such as pedestrian stackers or forklift trucks.
Different types of pallet racking systems are available such as wide aisle pallet racking which is commonly used with a counterbalance forklift or a reach truck for single pallet selectivity, through to pallet-live or push-back racking, which are designed for the densest storage capacity possible where the pallets are stored on roller beds to offer a first in-first out scenario or first in-last out scenario respectively.
RACK–MASTER STORAGE SYSTEMS LTD can help to find the right system to suit your needs AND your budget. Please contact us to arrange your free site survey and feasibility study so that we can assess your requirements and provide you with some options.
Systems We Can Offer You:
- Wide Aisle Pallet Racking
- Narrow Aisle Pallet Racking
- Drive-In Pallet Racking
- Pallet-Live Storage
- Push-Back Pallet Racking
- Carpet Racking
- Double-Deep Pallet Racking
- Coil Racking
- Heavy-Duty Racking
- Shuttle Racking
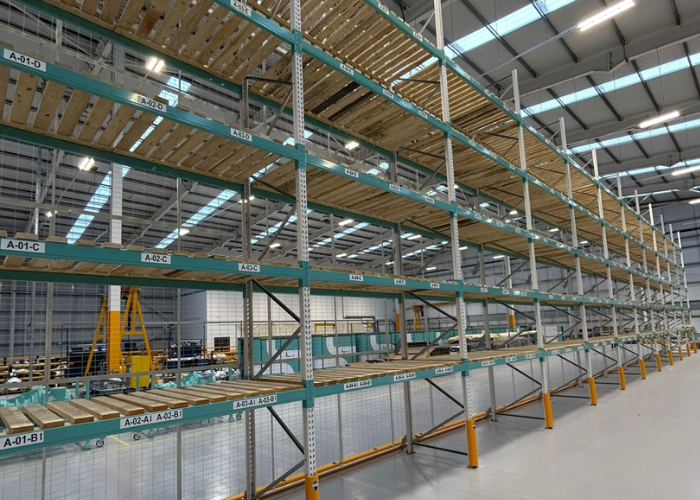
Wide Aisle Pallet Racking
The most common system found in most warehouses that require some form of pallet racking. Wide aisles (2.8M –3.5M) allow for the use of a variety of standard Forklift Trucks (such as a Reach or Counterbalance Truck) whilst maintaining single pallet selectivity meaning that any pallet within the system can be accessed at any one time. Modern Articulated forklift trucks (such as the Flexi / Bendi / Aisle Master) can work in aisles as little as 1.8M meaning standard wide aisle pallet racking is becoming ever more popular again for many warehousing applications.
Systems are available to suit virtually any pallet specification and this system is an excellent starting point for any new facility using pallets.
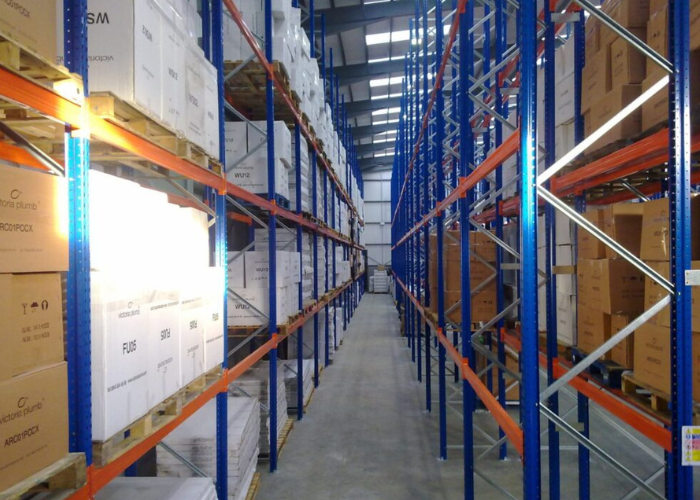
Narrow Aisle Pallet Racking
Essentially the same as Wide Aisle Pallet Racking but as the name suggests, operates in a much narrower aisle using specialist Forklift Trucks such as Narrow Aisle (NA) or Very Narrow Aisle (VNA) Trucks. Typical aisle dimensions
for these are in the region of 1.4M – 1.6M depending on the type of truck and the overall height of the system allowing for a much denser storage capacity to Wide Aisle Pallet Racking.
Systems are usually built with either underground Wire Guidance Systems or Angled Guiderails to ensure that the Forklifts negotiate the tight aisles with minimal damage to the racking.
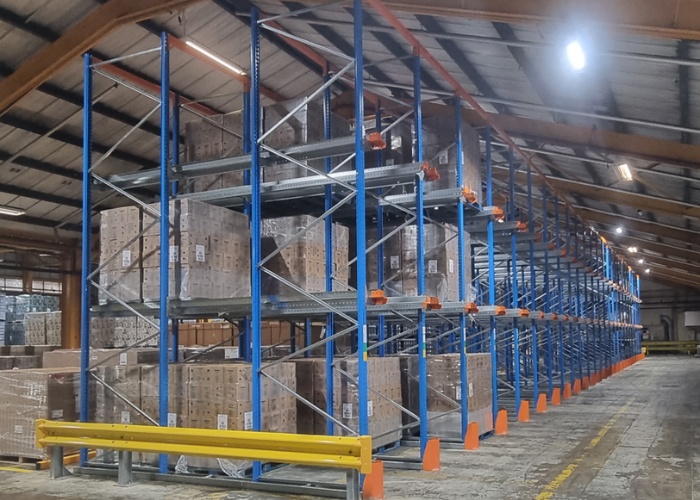
Drive-In Pallet Racking
This is the way to get the highest density of pallet storage capacity without block-stacking your pallets. In drive-in racking, a standard forklift drives into the lanes with the pallet and locates it onto cantilevered rails.
This system is suited to operations where you require a lot of storage of a similar product or where space is at a premium, such is in a cold store. This is because drive-in racking works on a ‘first in – last out’ basis (FI-LO) and is not ideal for single pallet selectivity as you have to clear a full lane at a time to get pallets from the back.
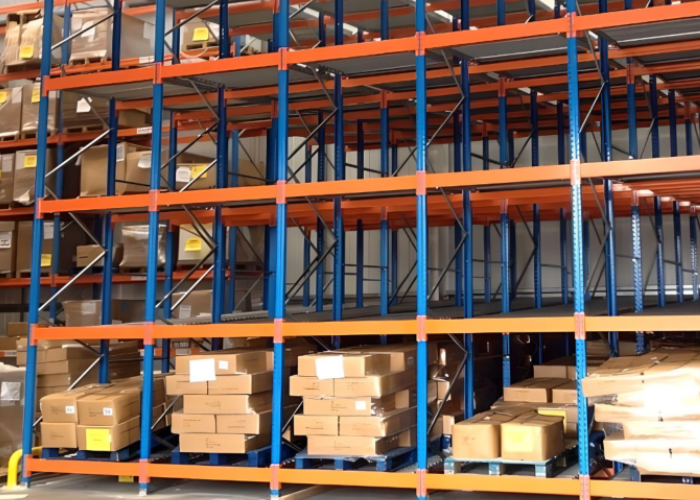
Pallet-Live Storage
A great way to get the highest density of storage capacity without block stacking your pallets, and whilst maintaining a good flow of products. This pallet racking installation works with two faces, a loading face and an off-loading face. Pallets are placed into roller lanes at the loading face and roll under the force of gravity to the off-loading face, so you get a ‘first in – first out’ (FI-FO) scenario ensuring good stock rotation. This can be accessed using most types of forklift truck.
This pallet racking system is suited to operations where space is at a premium but you are storing a product that needs to be rotated frequently (e.g. perishable products in the food industry). Pallet live storage also works well feeding into warehouse loading docks rather than block stacking pallets in lanes on the warehouse floor, enabling you to increase the capacity of your marshalling area.
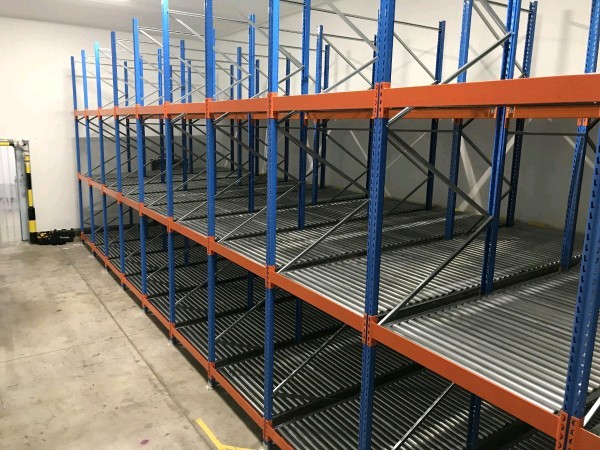
Push-Back Pallet Racking
A good way to get the highest density of storage capacity without block stacking your pallets as long as you don’t need to go more than four pallets deep. This system works with one access face which is used for loading and off-loading the system.
Pallets are placed in to roller or trolley lanes at the loading face which are then ‘Pushed-Back’ each time a fresh pallet is put at the front meaning you get a ‘First In – Last Out’ (FI-LO) scenario similar to Drive-In Racking. However, the difference between this and Drive-In Racking is that you can off-load by level rather than by having to empty a full lane.This can be accessed using most types of forklift truck.
This system is suited to operations where space is on a premium but you have storage of several different types of product that needs to be relatively easily accessed (such as in a freezer store).

Carpet Racking
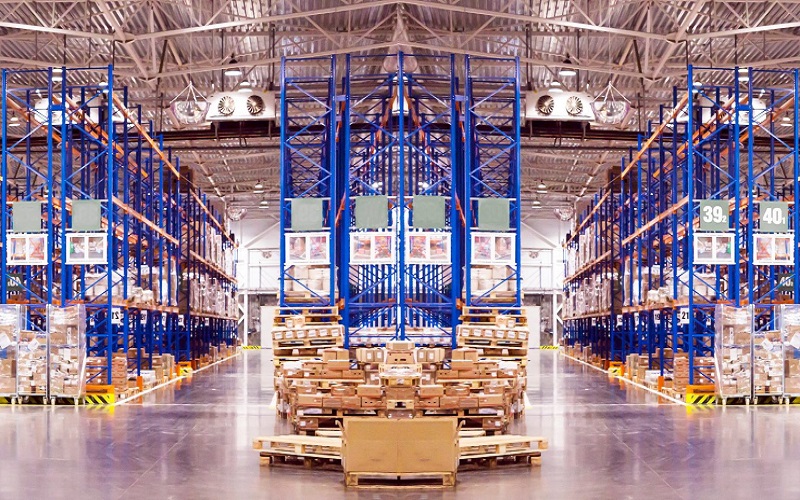
Double-Deep Pallet Racking
This works in a similar way to standard Wide Aisle Pallet Racking except that two standard bays are placed double-deep or back to back. Pallets are stored in the same way as wide aisle pallet racking except that they are stored two pallets deep and are accessed by specialist forklift trucks with ‘Telescopic Forks’ allowing them to reach in to the pallet location behind.
This system offers good storage capacities although single pallet selectivity is affected as you would need to remove the front pallet to gain access to the rear pallet which can dramatically increase picking times.
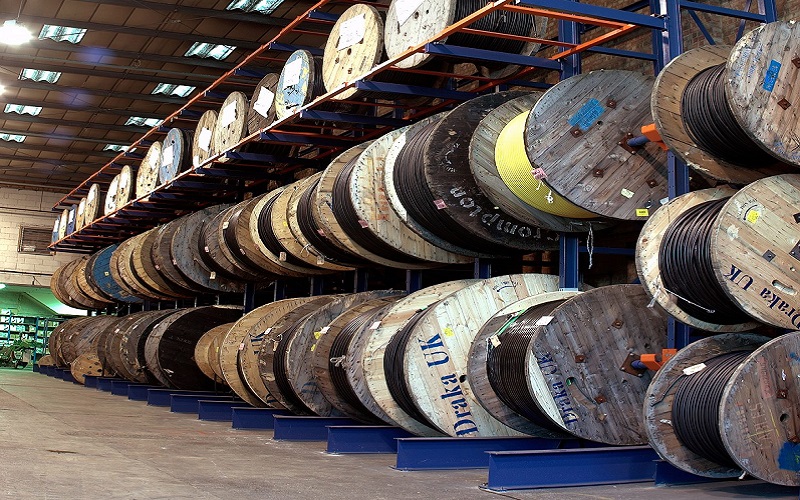
Coil Racking
There are three ways of storing Coils. Either ‘Eye to the Sky’ meaning that the coil is located on a pallet on its side or using a ‘Coil Cradle’ meaning that the coils can be located in to a system using a ‘Boom’ attachment on a forklift jousting through the eye of the coil. You can also store them on central spindles which allow the coil to rotate for uncoiling whilst being stored. Coils stored ‘Eye to the Sky’ are usually stored in standard pallet racking but coils stored side on are stored using a coil cradle together will standard pallet racking allow for single coil selectivity and doing away with pallets.
This system is good for manufacturing plants that use steel coils during their manufacturing processes and gets the coils in a position where they can be accessed easily and located straight in to an industrial machine without having to change the orientation of the coil or remove a pallet.
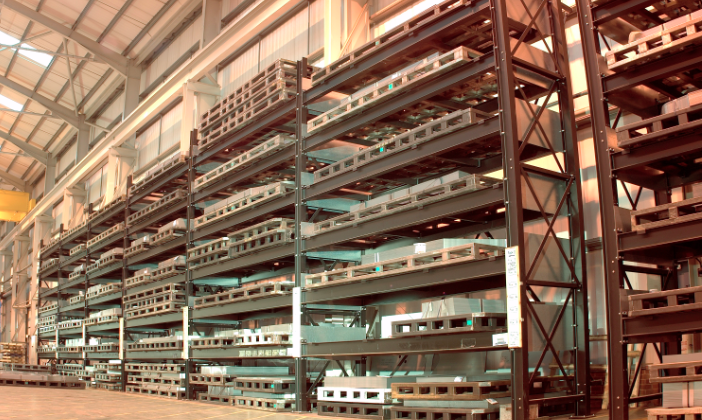
Heavy Duty Pallet Racking
This system is similar to standard Wide Aisle Pallet Racking but where the standard system falls down because it can’t get to the required weight capacity, Heavy Duty Racking steps up to the plate. This is for bay loadings of typically 20,000Kgs plus or loads per level in excess of 4,000Kgs (depending on level overall dimensions). The way we achieve this is by moving away from standard manufactured racking parts and going to Structural Universal Beam (UB) Sections more commonly found in buildings. These are bespoke designed to your specific loads and environment to achieve the required capacity. These are usually accessed by High Capacity Counterbalance Forklifts.
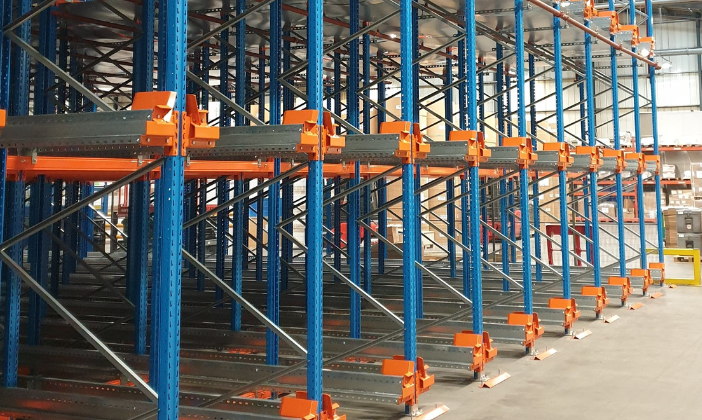
Shuttle Racking
This system is like a combination of Drive-In Racking, Push-Back Racking & Pallet Live Storage. The structure is very similar to Drive-In Racking in the fact that there are no rollers / dynamic flow beds and that the pallets are stored flat, however, the forklift never enters the lane. Instead the forklift positions a ‘shuttle device’ at the start of the lane into a runner section that runs underneath each pallet lane. The shuttle device is programmed to either bring the pallets back to the front of the pick face (as with Push-Back) or to the rear of the system (as with Pallet Live) meaning you can have ‘First In – First Out’ (FI-FO) stock rotation with multiple pick faces or ‘First In – Last Out’ (FI-LO) stock rotation with a single pick face. The higher the throughput of the system increases the quantity of shuttle devices that you would have running at any one time.